Blister Machine DPP260Ki-2
Brief introduction
All the main parts are made of premium stainless steel and alu-alloy material and machined by advanced high-precision CNC tooling machines.
Description
Customer Case
Featured Products
. Equipped with automatic format locking, the positioning system achieves an extremely straightforward format changeover (new).
. In the sealing station, when the machine stops, the heating sealing mold can rise up automatically to prevent hot air from getting into the blister pockets so that medicine effectiveness is preserved.
. Sealing pressure adopts the gas-hydraulic pressure cylinder, so the pressure can be set freely according to the sealing area (commonly, a larger sealing area requires higher pressure) (new).
. All the main parts are made of premium stainless steel and alu-alloy material and machined by advanced high-precision CNC tooling machines.
. Accommodates two forming material reels. One of the reel’s diameters can reach up to 600mm; if it equips the waste material trimming cutter(optional), it could allow production runs of approximately 90 minutes, therefore, reducing the material replacement frequency.
. This machine is equipped with an integrated forming material splicer to enhance efficiency during material replacement.
. Using a fast lock method enables the replacement of lidding material easily within 10 seconds.
. Add a perforation station to separate the perforation from the embossing station. Conventionally, perforation and embossing remain in one station, but this will influence the clarity of each (optional).
. The blister length can be set freely through Touch Screen User Interface, which reduces the time for a format changeover.
Gallery
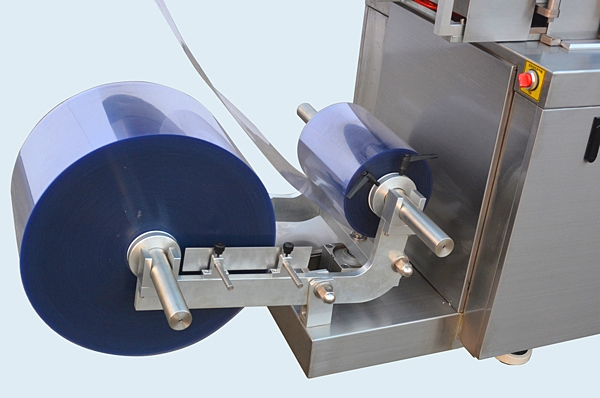
The forming material reel of up to 600mm in diameter.
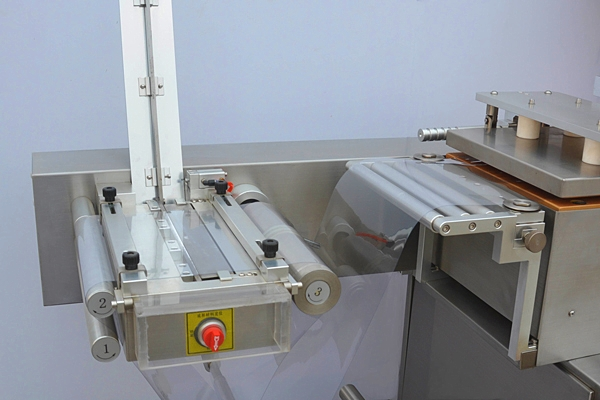
Equipped with integrated forming material splicer.
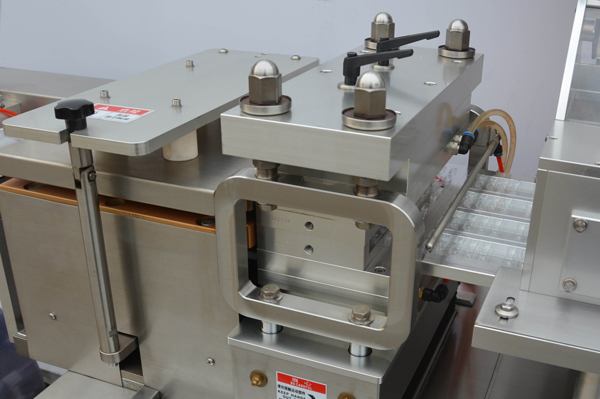
The upper and lower plates adopt contact heating method that significantly reduces the forming temperature. Thus the shrinkage, deforming of packaging material and power consumption are minimized.
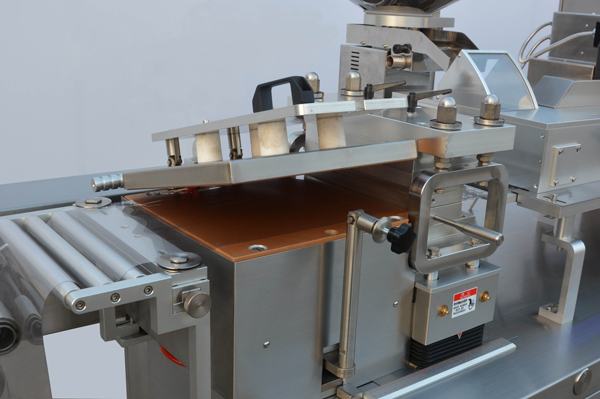
The contact forming heating station can be opened up for cleaning very conveniently.
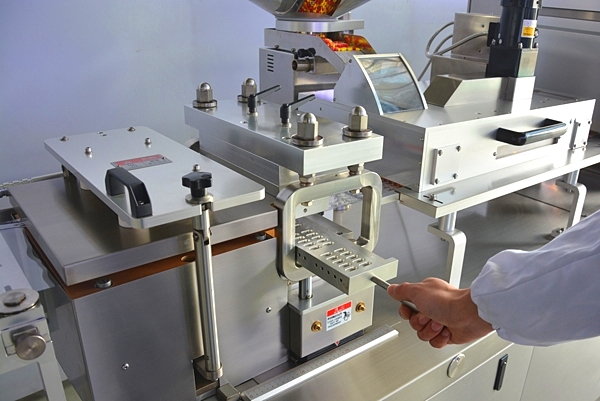
Equipped with automatic format locking, positioning system, achieves extremely straightforward format changeover.

The universal feeder is capable of feeding almost all items such as capsules, flat tablets, oval tablets, capsule tablets, triangular tablets or other various shapes.

The flat tablets, capsules or oblongs are fed via tracks or tubes into the aluminium blisters.

Integrated product inspection system with color camera can reject faulty blisters automatically (optional).
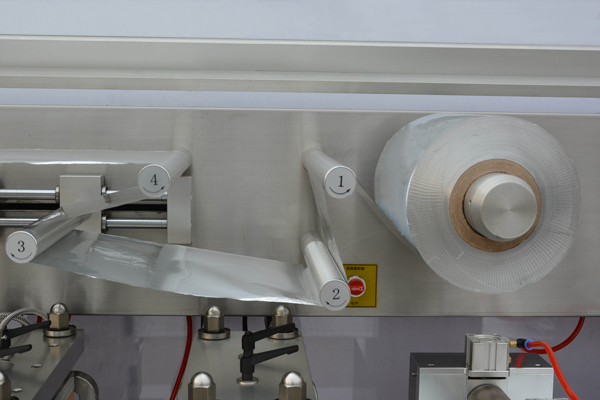
The lidding material loader adopts a fast lock mechanism, enabling replacement of lidding material easily within about 10 seconds.

All of the guide rollers are labeled with a sequence number and placement direction, making it very easy to guide the film and lid foil through the machine.

Add one more station, to separate the perforation from the embossing station. Conventionally, perforation and embossing remain in one station, but this will influence the clarity of each.
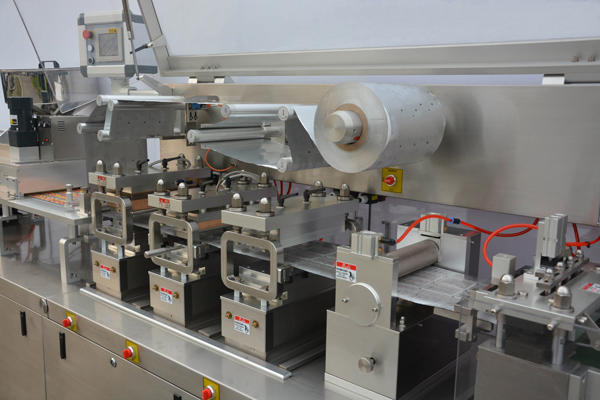
The material drag system adopts a precise servo motor to achieve stable, accurate running. The blister length can be set freely through Touch Screen User Interface, which reduces the time for a format changeover.
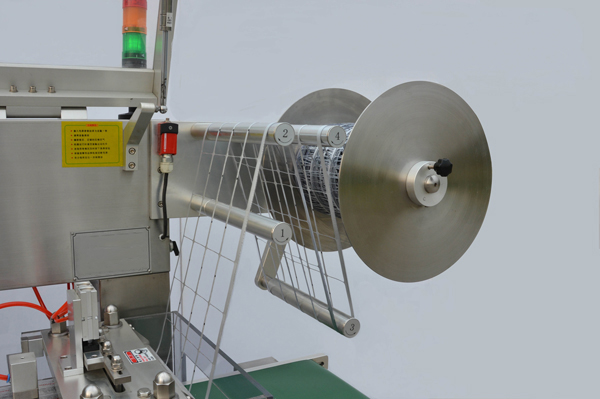
The waste material winding mechanism.
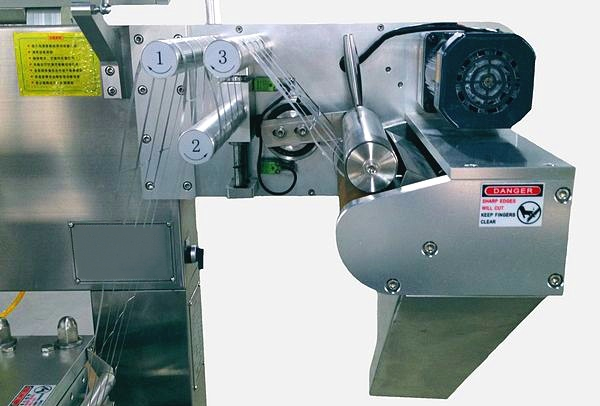
The waste material trimming cutter (optional).
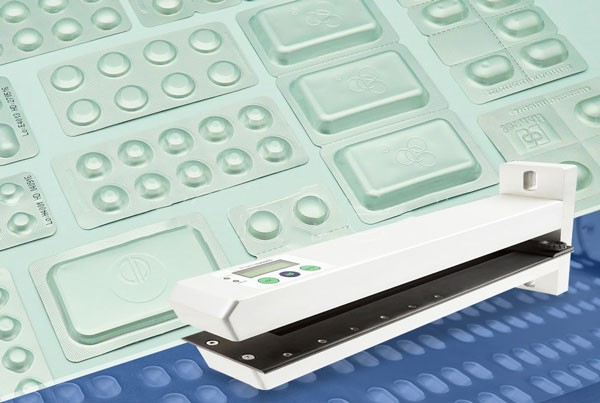
Pinhole detection system for quality assurance of blister packaging (optional).
Main Technical Parameters
If you are interested in this, please contact me: Nana Zhang
Cell Phone: 0086-15800947006
https://medigrade.en.made-in-china.com/ made-in-china.com
. In the sealing station, when the machine stops, the heating sealing mold can rise up automatically to prevent hot air from getting into the blister pockets so that medicine effectiveness is preserved.
. Sealing pressure adopts the gas-hydraulic pressure cylinder, so the pressure can be set freely according to the sealing area (commonly, a larger sealing area requires higher pressure) (new).
. All the main parts are made of premium stainless steel and alu-alloy material and machined by advanced high-precision CNC tooling machines.
. Accommodates two forming material reels. One of the reel’s diameters can reach up to 600mm; if it equips the waste material trimming cutter(optional), it could allow production runs of approximately 90 minutes, therefore, reducing the material replacement frequency.
. This machine is equipped with an integrated forming material splicer to enhance efficiency during material replacement.
. Using a fast lock method enables the replacement of lidding material easily within 10 seconds.
. Add a perforation station to separate the perforation from the embossing station. Conventionally, perforation and embossing remain in one station, but this will influence the clarity of each (optional).
. The blister length can be set freely through Touch Screen User Interface, which reduces the time for a format changeover.
Gallery
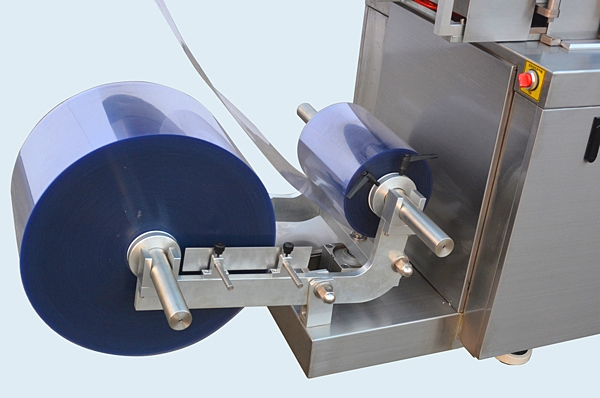
The forming material reel of up to 600mm in diameter.
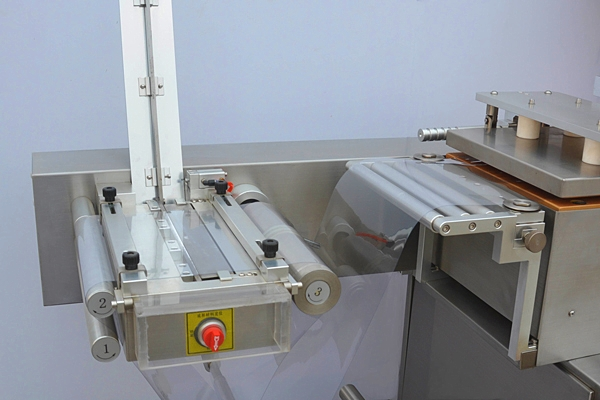
Equipped with integrated forming material splicer.
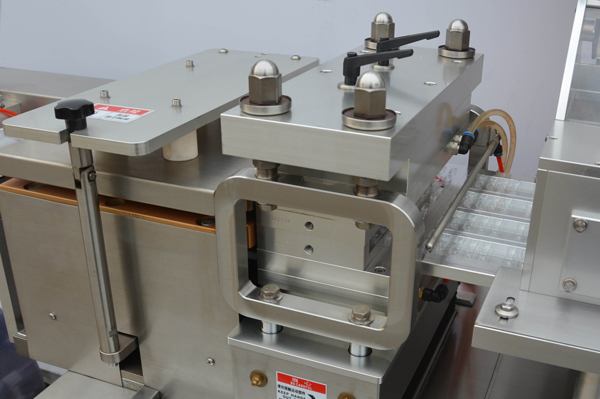
The upper and lower plates adopt contact heating method that significantly reduces the forming temperature. Thus the shrinkage, deforming of packaging material and power consumption are minimized.
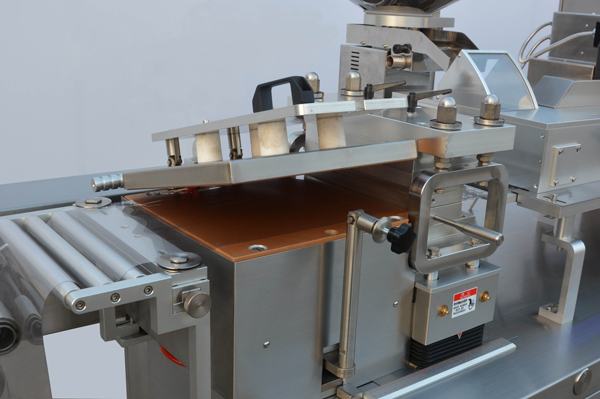
The contact forming heating station can be opened up for cleaning very conveniently.
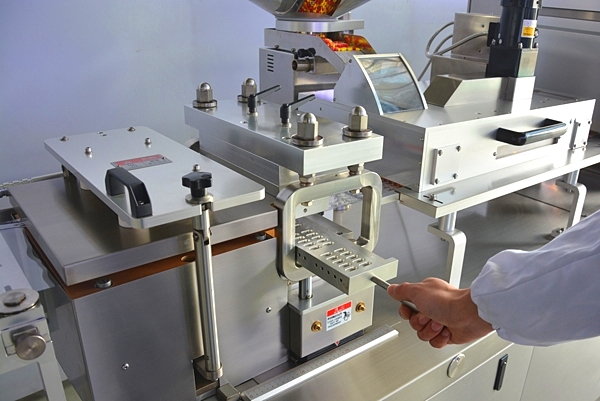
Equipped with automatic format locking, positioning system, achieves extremely straightforward format changeover.

The universal feeder is capable of feeding almost all items such as capsules, flat tablets, oval tablets, capsule tablets, triangular tablets or other various shapes.

The flat tablets, capsules or oblongs are fed via tracks or tubes into the aluminium blisters.

Integrated product inspection system with color camera can reject faulty blisters automatically (optional).
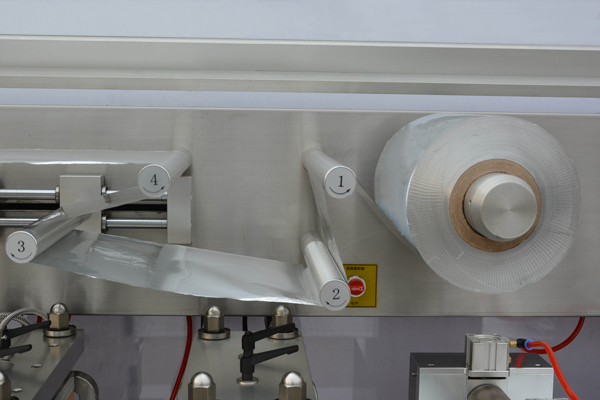
The lidding material loader adopts a fast lock mechanism, enabling replacement of lidding material easily within about 10 seconds.

All of the guide rollers are labeled with a sequence number and placement direction, making it very easy to guide the film and lid foil through the machine.

Add one more station, to separate the perforation from the embossing station. Conventionally, perforation and embossing remain in one station, but this will influence the clarity of each.
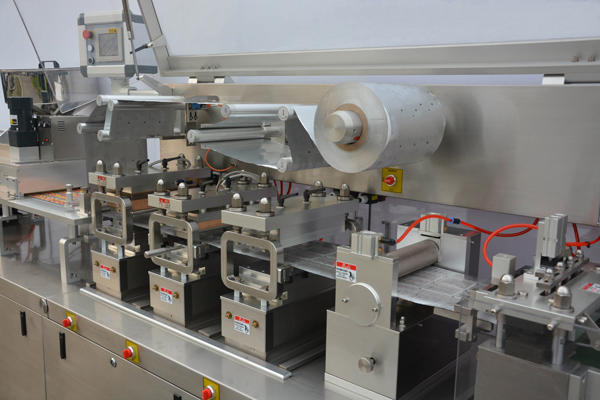
The material drag system adopts a precise servo motor to achieve stable, accurate running. The blister length can be set freely through Touch Screen User Interface, which reduces the time for a format changeover.
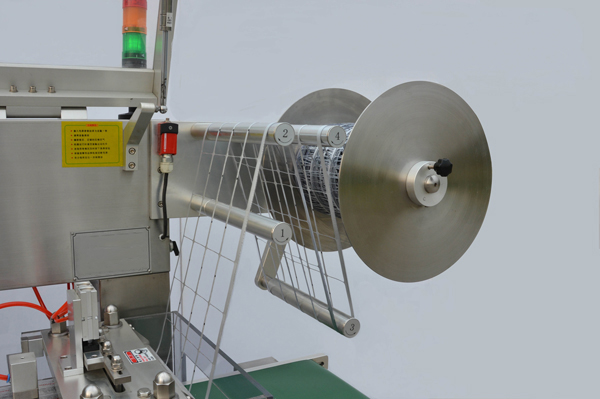
The waste material winding mechanism.
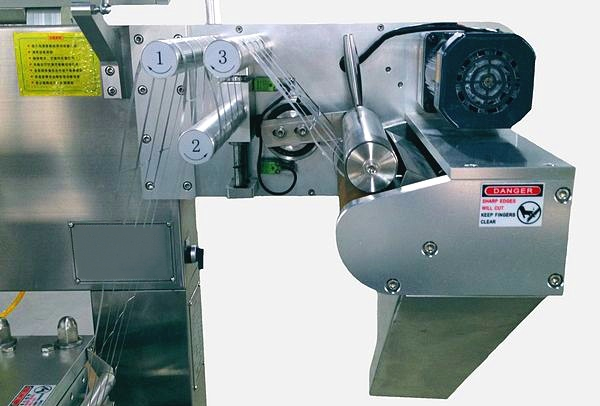
The waste material trimming cutter (optional).
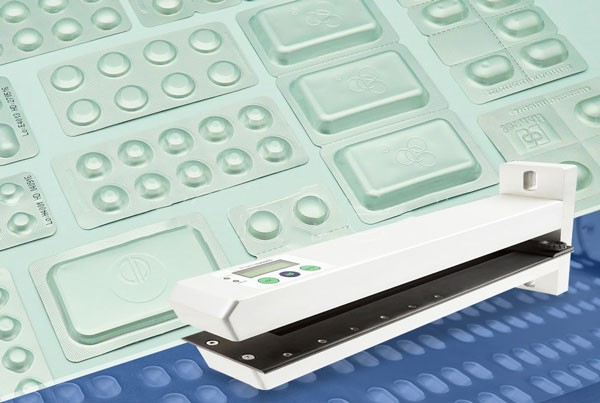
Pinhole detection system for quality assurance of blister packaging (optional).
Main Technical Parameters
Max. Speed: | alu/alu 40punches/min. alu/pvc 60punches/min. |
Max. Forming Area: | 250×158mm |
Max Forming Depth: | 12mm |
Material: | Max. width 265mm |
Machine Power: | 9.6kw |
Machine Dimension: | 4200×740×1700mm (4 stations) 4450×740×1700mm (5 stations) |
Machine Weight: | 1800kg (4 stations) 1950kg (5 stations) |
If you are interested in this, please contact me: Nana Zhang
Cell Phone: 0086-15800947006
https://medigrade.en.made-in-china.com/ made-in-china.com
Customer Case
Featured Products
All the main parts are made of premium stainless steel and alu-alloy material and machined by advanced high-precision CNC tooling machines.
Pharmaceutical Research and Development laboratories, Clinical trials, Stability studies, Package development, Marketing, samples, Pharmaceutical production, and packaging departments.
Thanks to rotary sealing style (alu-pvc) and larger tropical aluminum forming and sealing area, the machine archives high output, for the size of 98mm*70mm, the output can up to 180 blister cards/minute (DPH260H3) and 270 blister cards/minutes (DPH350H3).